The Vestas plant in Brandenburg is already closed, and now Nordex in Rostock is also closing for good. But satellite images show: While the German wind power industry is languishing, the sector in Denmark is growing gigantically.
“Economy from above” is a collaboration between WirtschaftsWoche and LiveEO. This is a translation of the original article written in German by “Konrad Fischer“. Access the original article here.
The employees at the Nordex plant in Rostock fought for their jobs until the very end. As recently as April, they staged a large-scale demonstration to avert the threat of closure. It was no use: At the end of June, the last rotor blade left the plant in the port area, 530 employees are now transferring to a transfer company, if they have not already started looking for other jobs. They will suffer the same fate as the 500 employees at Vestas’ Lauchhammer plant in Lusatia at the end of February. There, too, the factory was closed, and there, too, overcapacities on the market and location competition with the Far East are said to have been to blame for the misery.
Employees won’t have to travel that far for new jobs – at least if they speak a little Danish. While the wind power industry in Germany has experienced a decline in recent years that is fatally reminiscent of developments in the solar industry, the opposite story is playing out just north of the country’s border: The Danish wind power industry is booming, as shown by exclusive satellite images from LiveEO.
Almost every superlative that the industry is currently reporting is taking place in Denmark. The largest rotor blades, the most powerful generators, the largest foundations: All made in Denmark. Almost half of the total offshore energy installed in Europe, as recently calculated by a Danish industry association, was handled via the port of Esbjerg on the west coast of Jutland.
.webp)
.webp)
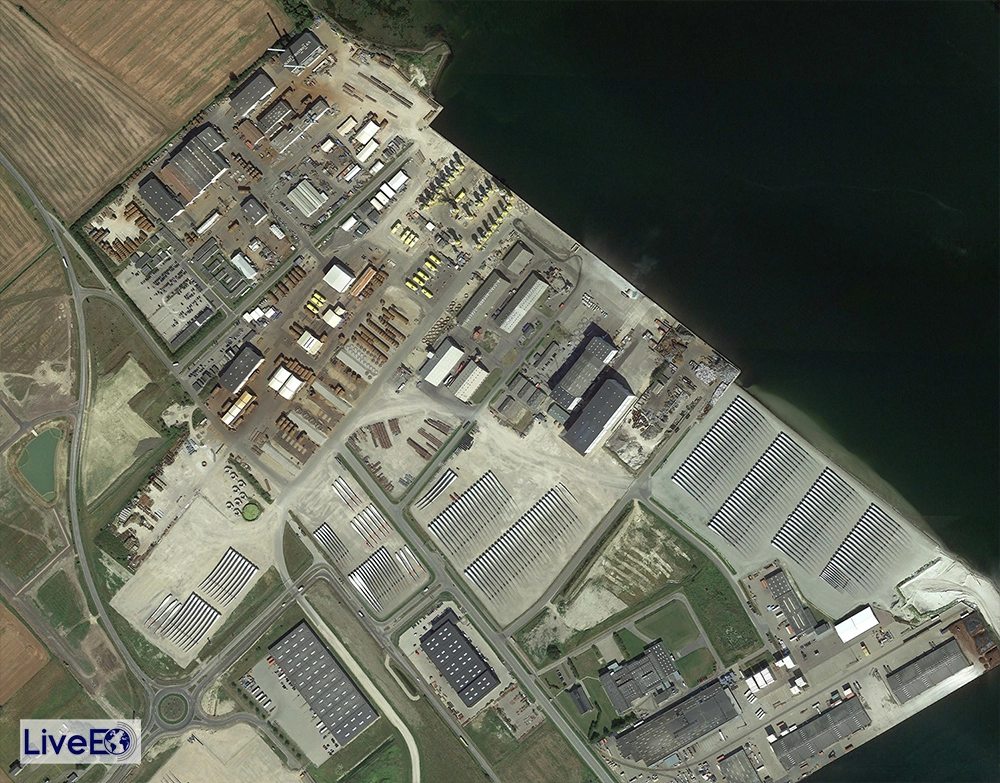
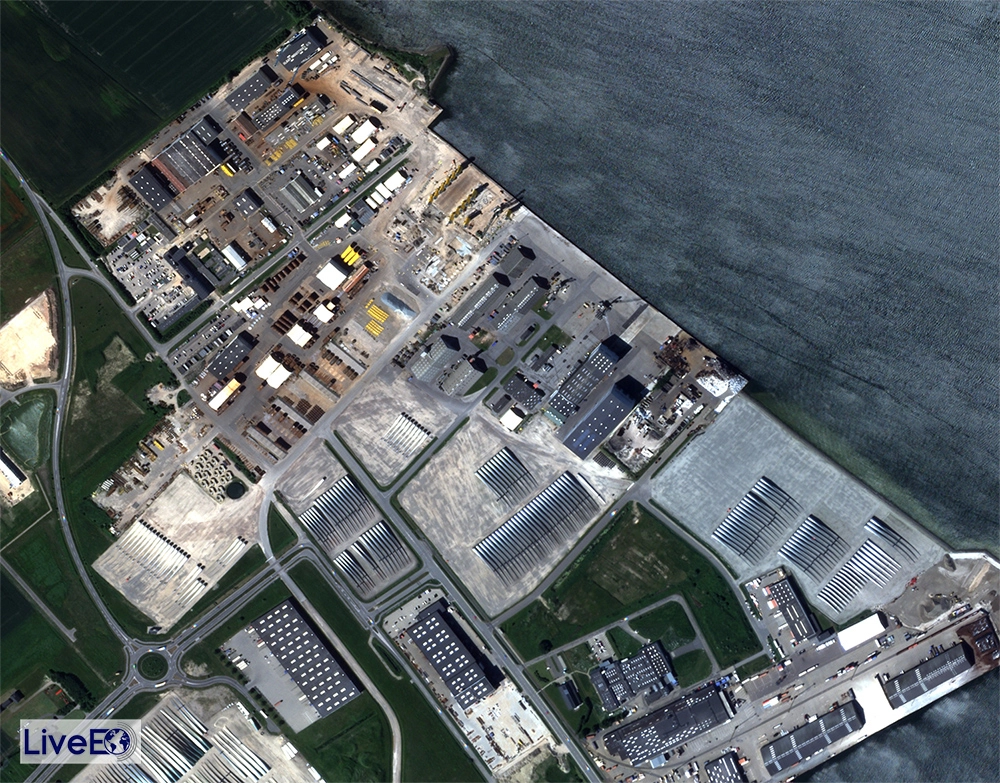
The satellite images show just how impressive the development actually is. At the center of the Danish wind industry is the port of Esbjerg, whose location is ideally suited to reach the offshore facilities in the North Sea. It is from here that most of the components for the farms on Danish soil as well as those in British waters are delivered. The construction of the German wind farm Kaskasi – the only German offshore farm to be connected to the grid this year – is also being handled from here.
The satellite images show how much wind power has come to dominate the port: Only 15 years ago, only a single tower of a wind turbine is visible, otherwise smaller factory buildings and tanks dominate the picture – next to a lot of greenery. Then, over the years, the area of the port is expanded by more than a third, the new areas as well as all green spaces are now occupied by rotor blades and other wind power components.
Not yet visible, but long in the planning stages, is the next stage in the development of the Esbjerg wind power cluster. By 2026, the city will fill in another L-shaped area in the south of the harbor, which will expand the harbor area by another 500,000 square meters, exclusively reserved for the expansion of the wind energy industry.
But even beyond the port of Esbjerg, the wind energy industry in Denmark has long been an important sector of the economy. After all, 2.3 percent of all private employees in the country are employed here. And thus dependent on a very special growth logic. The wind industry is more cyclical than any other. With each new generation of rotors, the turbines get bigger. And with them, all their components become larger, heavier and more complicated to transport. The selection process among the factories is correspondingly sharp: A production facility that may have been perfectly suitable for 80-meter-high rotors is no longer usable for 120-meter-high turbines, for example, because the next freeway access ramp can no longer be expanded and the ground must not be loaded with additional weights.
At least for the time being, however, most Danish locations are apparently well equipped for the gigantomania of the industry: For all components of the 15-megawatt class, which will be the measure of all things in the construction of offshore parks in the coming years, there are manufacturing sites in the country. For example, there is the port of Aalborg, on the east coast of Jutland.
.webp)
.webp)
.webp)
.webp)
.webp)
At the left edge of the picture, you can see the factory buildings of Bladt, the global pioneer in the construction of monopiles, the concrete and steel structures used to anchor wind turbines in the seabed on the high seas. In 2018, the Group began to convert its site so that the components manufactured here can also support wind turbines in the 15-megawatt class, and the first models are currently being delivered. Over the years, it is clear to see how more and more pylons are being stored on the outdoor site, and the dimensions of each individual pylon are also growing steadily.
To that end, Bladt has apparently taken over space from its southern neighbor: Siemens Gamesa, which has maintained large manufacturing facilities in Denmark since buying its competitor Bonus Energy in 2004. In Aalborg, as can easily be seen in the pictures, rotor blades are manufactured. Over time, it can be seen how each of the blades so accurately stored there is gradually growing in size. The latest satellite photos also show that there is still plenty of room for even the most advanced class products. In April, the company announced that it would begin production of the latest generation of rotor blades, each 115 meters long. Siemens Gamesa also operates the world’s largest indoor test center for rotor blades here, which is also open to other manufacturers.
The major Siemens competitor Vestas has secured two entire bays in Denmark in order to be prepared for the age of offshore giants. The rotor blades are manufactured in Nakskov in the southwest of the island of Lolland, and the hubs in Lindø north of Odense on the island of Funen. These are the components where the rotor blades are connected to the tower and where the wind movement is converted into electrical energy.
Viewed from space, the components look a bit like angular white insect bodies. The models seen in the pictures are probably still those of the previous generation (10 megawatts); only in March did Vestas announce that it would also build the hubs of the 15-megawatt generation here, which are to be delivered from 2024. The company is currently producing a first prototype of the turbines, which will soon be tested at the Danish national test center in northern Jutland.
.webp)
.webp)
.webp)
.webp)
.webp)
.webp)
In addition to rotors, hubs and monopiles, the manufacturers are now only missing one component for the construction of offshore turbines: the tower. Here, too, the two leading manufacturers are to be found in Denmark. Like Valmont, which manufactures its turbines a good 20 kilometers north of Flensburg in Rødekro, its competitor Welcon has also settled inland. In the village of Give, around 50 kilometers east of the central port of Esbjerg.
Here, too, the components have grown along with the dimensions of the wind turbines. How long this will be feasible at this location far from the sea, however, is debatable. It is true that the satellite images show that a highway was built a few years ago that runs directly past the site. But this does not change the distance to the sea.
Until a few years ago, Siemens Gamesa manufactured its rotor blades for onshore turbines in the neighboring town of Brande. However, this is no longer profitable, similar to the German Vestas site in Lauchhammer. So the factory switched to the very heavy but less large hubs – which were previously manufactured in Cuxhaven. The tower manufacturer Valmont has already secured a plot of land in the port of Esbjerg so that it can load its next-generation components directly onto ships. So structural change is also taking place at Danish wind power sites, albeit with one difference to what is happening in Germany: for most of the factories and jobs that are disappearing, new, larger sites are being built elsewhere in the country.